
ARCXIS Inspection Services
ARCXIS offers over 100 different types of residential inspections from inspecting the site prior to placement, to the pour of the foundation and construction of the frame and right through to final quality assurance: code, structural, mechanical, electrical, plumbing and cosmetic. All inspections are conducted by trained and certified inspectors.
Pier Inspection
Typically a Pre-Placement and Placement inspection of Piers on the same day. Inspection of the drilling of the holes for the correct size diameter and the depth stated by the Soil Report documentation. Inspection of the makeup of the rebar being installed into the hole. Inspection also covers the concrete being poured into the piers.
Site Preparation
Inspection is a site visit to verify the foundation site work has been completed and prepared to the engineering specification of the foundation design. It involves our inspection team verifying proper drainage for the entire section. This is typically followed by an engineering report informing the builder to the status of the site and the possible work needed from the builder/developer to ensure proper foundation structural integrity. This inspection can also cover the foundation pad as well.
Plumbing Rough
Inspection of the PVC piping which plumbers install in and under the slab. The inspection is to insure a proper slope fall of the pipes and the proper connection of the fitting. This inspection can be done with water in the pipes to verify there are no leaks present before being covered with foundation dirt.
Sub Surface Drainage
This service is the inspection of a French Drain application. This French Drain can either be during a Walk-Out Basement construction or a French Drain for backyard water removal. Either of these applications could be covered with this type of inspection.
Pre-Placement Inspection
Typically our first inspection for the builder. This inspection makes sure the builder constructed the slab exactly like our foundation engineering dictated to the builder. This covers beam depths, strand orientation, strand count, proper amount of chair spacing, rebar, etc. Builder should run a string from each corner to corner to help inspector perform his job better.
Deep Beam Pre-Placement
Inspection of the lower part of a beam that cannot be poured on the same day. This usually covers the makeup of the rebar and the extension rebar connecting the deep beam to the foundation to be poured later above the deep beam below.
Footer Pre-Placement
Inspection to cover the lower part of a double or triple pour system. This could be the lower part of walk out basement foundation or the lower part of a retaining wall. This inspection covers the makeup of the rebar and extensions of rebar or anchoring system of what will tie in later on top of the footer.
Stem Wall Pre-Placement
Inspection covers the second part of a three pour system. This is the vertical concrete structure that connects the lower concrete system with the future upper concrete system. This could also be assigned on a retaining wall makeup. This inspection covers the makeup of rebar and the extension anchoring system of what will be attached above at a later time.
Placement Inspection
Typically our second inspection on our foundation design. This inspection insures the locations of each truck within the foundation system. The inspector makes sure the foundation labor or turn-key companies do not request too much water in the mix. This is the most important inspection in the foundation to make sure our foundation will be structurally sound for many years to come.
Deep Beam Placement
This inspection covers the pouring of the concrete in a Deep Beam system. It follows the same process as the Placement Inspection except it is for the Deep Beam part of the foundation system.
Footer Placement
This inspection covers the pouring of the concrete in a Footer system. This could be the lower portion of a three part pour or the base of a retaining wall system. It follows the same process as the Placement Inspection except it is for the Footer or base of a Retaining Wall part of the foundation system.
Stem Wall Placement
This inspection covers the pouring of the concrete in a Stem Wall system. This could be the vertical portion of a three part pour or the pouring of a retaining wall system. It follows the same process as the Placement Inspection except it is for the vertical Stem Wall part of the foundation system.
Elongation Inspection
This inspection happens after the pouring of the concrete. The post tension companies get notified from DPIS that it is OK to stress the cables. Once the cables have been elongated (stressed), DPIS goes out and verifies the cables have been elongated to a required minimum distance. This is done by the inspector measuring how far the painted cable has moved outside of the form of the foundation system.
Frame - Sub-Floor Only
This is an added inspection when residential construction presents a wood flooring system tied to a foundation system. We must inspect this framing system before it gets to a point where we cannot see this portion of the construction at a later date.
Blocking Inspection
Inspection of the Frame Only system concentrating on air infiltration floor blocking and chase fire blocking. This inspection should be a consultative inspection to allow the construction to move to the next stage. This inspection helps retain your framer. The items caught on this inspection can be re-inspected at the FrameNet stage.
Shear Wall Inspection
Inspection of the shear wall system and outside structural wall bracing system. This inspection should happen before the Drainage Plane is installed.
Clip & Strap
Inspection of the Clips & Straps for wind speed call outs on all product outside of the TDI Windstorm certification area. This is used when a city has mandated a design of a higher wind speed and we are verifying our design.
Frame - Structural
Part 1 of 2-Stage FrameNET. Consulting type inspection. This inspection covers per plan construction, sheathing nailing pattern for wall brace compliance and air/fire blocking. This inspection does not include Electrical, Mechanical, and Plumbing call outs. That is covered in the FrameNET.
Mechanical Only
Inspection of the Mechanical system only at the Rough Frame Stage.
Electrical Only
Inspection of the Electrical system only at the Rough Frame Stage.
Sheathing Inspection
Inspection of the outside Sheathing system for proper nailing and sufficient wall bracing per framing design. This inspection is bundled with our Wall Brace Design and certifies your wind speed requirement has been met.
Drainage Plane Inspection
Inspection to look at the Drainage Plane system of the home. This inspection is typically called in when the builder wants to move on with cladding the home before the frame inspection stage has been cleared fully
Frame.NET
This inspection is our most thorough and time consuming inspection for our builders. This inspection covers structural, mechanical, electrical, and plumbing. The items within this inspection are tracked for the builder and issued as a report for them to see what items are being called out. This inspection must pass before moving on to the sheetrock stage, especially the structural part pertaining back to our engineering design.
Insulation Inspection
Insulation Inspection to verify the energy efficient components the builder is installing to comply with either IECC code, HERS, IC3, Energy Star or other program guidelines.
EFL Certification Services
ARCXIS is a master EFL certifying entity. If the builder is wanting to comply with the Environments For Living program, ARCXIS can be a company to help builders verify and perform the required testing for the program and supply the program with the confirmed rating for the builder EFL documentation.
IECC Code Certification Services
Every home following the IECC code compliance must either be better than the chart in the code book. This method is Prescriptive and can ultimately cost the builder more money to comply. Utilizing the Performance can help the builder comply and still be in control of what they deliver to the consumer. Each of these method still require a plan analysis, insulation verification and duct and blower door testing on each address.
HERS Certification Services
ARCXIS is the largest RESNET HERS rating provider in the country. Contact ARCXIS to set up a consultation with any of our sales reps to see what it takes to deliver a HERS rated home. Each HERS rated home must go through a HERS modeling software, have every installed energy component verified at Insulation stage and go through duct and blower door testing for confirmation.
Energy Star Certification Services
ARCXIS is the largest Energy Star provider in the country. Contact ARCXIS to set up a consultation with any of our sales reps to see what it takes to be Energy Star Certified. Each Energy Star Home must meet the performance and prescriptive standards developed by the EPA. Each of these also require the installation and verification work to be an Energy Star certified contractor.
Indoor airPLUS Certification Services
ARCXIS has been an EPA Indoor airPLUS Leader of the Year several times since 2011. We have certified more Indoor airPLUS homes and units than any other provider in the country. IAP builders and homes take the health of their occupants seriously and we verify that all the measures of the program are being adhered to.
WaterSense/HERS H2O Certification Services
ARCXIS is a provider of both the WaterSense (EPA’s water efficiency program) and HERS H2O (RESNET’s water efficiency scoring system) certification programs. The two now work hand in hand and by achieving a HERS H2O score of 70 or less you can earn the WaterSense certification. Water conservation is becoming more and more important to the sustainability of our communities and ARCXIS is proud to provide this certification.
Stucco Inspection
Lathe or Scratch Coat Stages - Lathe stage inspection covers making sure the material behind the stucco is creating a secondary drainage plane and is installed like a roof and securely fastened. Scratch Coat Stage verifies expansion joint placements and screed edge on bottom of the stucco system for proper drainage.
Drywall Inspection
This inspection covers securing the drywall properly. This inspection can add some structural integrity and possibly increase firewall makeup. If installed a certain way and verified by our inspector this can be used as a possible wall bracing method.
Flatwork Inspection
This inspection covers any type of concrete pour that is not a structural component of the building. This can include sidewalks, or keyed in floors for the garage and basement floors. This is typically a Pre-Pour and a Pour on same inspection day.
Comfort / Building Science Forensic
This inspection is used when a builder needs to figure out comfort, moisture or high utility bills. This inspection typically involves a through investigation using an Infrared Thermal camera along with blower door and duct blaster equipment. This inspection can also involve Advanced testing (CFM) as well to verify comfort complaints.
Energy Final
Energy Final testing including Blower Door and Duct Blaster Testing. These testing parameters are to meet or exceed the limits in the Proposed calculation for whatever energy program level the builder desires. Code, HERS, Energy Star, EFL, etc.
Green Final
There are many Green building programs in the industry. ARCXIS has helped build several of them across the country. The Green Final Inspection covers verification of any of the green items the builder is placing on each of their homes. These verified components go into the scoring tool to comply with the respective green building program.
Thermal Inspection
A thermal inspection utilizes an infrared camera to inspect for deficient or missing insulation, water intrusion, and / or overheated electrical components. Thermal inspections are currently not permissible as part of ENERGY STAR certification; however, they are admissible for improved insulation grading in a HERS Rating.
Advanced Testing
This inspection is for the advanced extra testing that ARCXIS can provide. This includes CFM Flow Measurements, Static pressure at the supply and return plenum and the room to room pressure. This testing follows the ACCA QI5 Standard.
Final Quality Assurance
Time of this inspection is previous to the buyer walk at the Final stage of the home. This inspection covers all items that pertain to the home being ready to close and buyer moving in. This inspection covers everything from health and safety to cosmetic. The buyer satisfaction statistics from this inspection is what keeps our clients coming back to us time after time.
CSI Inspection
This is a Final inspection on the plumbing system only. This is per CSI inspection protocol and must be done by a specially certified inspector or under a plumbing certified engineer.
Bank Draw Inspection
This is an inspection to verify the construction stage completion percentage of the job. This is typically order by the bank to verify if the amount of money being asked from the builder matches the amount appropriate to stage of construction completion.
Forensic Structural Inspection
This is an inspection to cover a job that is already complete and has a potential problem on either the structural side or the comfort side. We send an expert or a team of experts out to the address to figure out the problem and complete a report informing the builder of the exact items that need to be corrected to fix the structural aspects in the house.
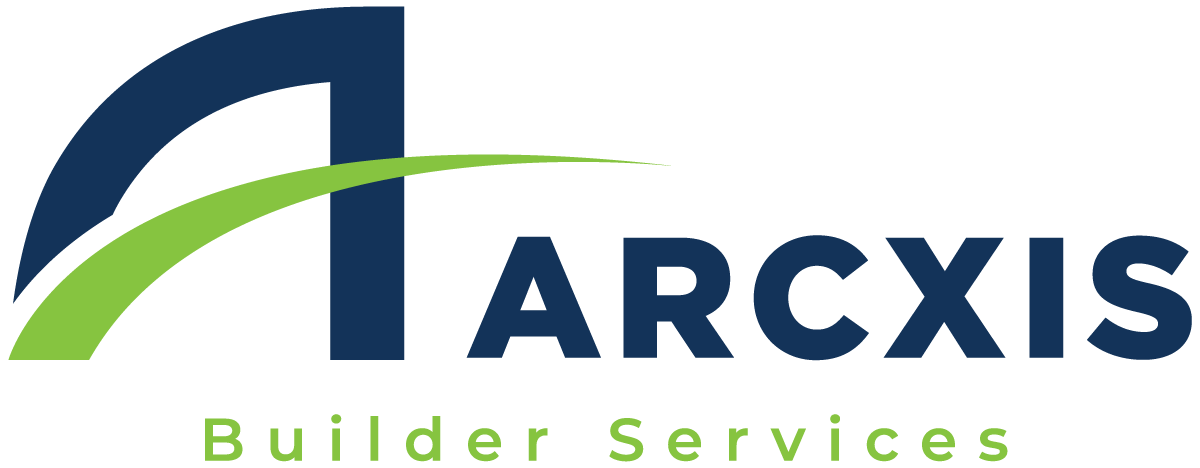